The working principle of centrifugal pump is: centrifugal pump so water can be sent out due to the role of centrifugal force. Pump before work, the pump body and the inlet pipe must be filled with water to form a vacuum state, when the impeller rotates quickly, the blade to promote rapid rotation of water, rotating water from the impeller in the centrifugal force of the fly, the pump of water After being thrown, the central part of the impeller forms a vacuum area. Suwon's water pressure in the air pressure (or water pressure) under pressure through the pipe into the water pipe. This endless cycle, you can achieve continuous pumping. It is worth mentioning that: before starting the pump must be filled with water to the pump casing before starting, otherwise it will cause the pump body heat, vibration, reduce the amount of water, causing damage to the pump (referred to as "cavitation") Cause equipment accident! Many types of centrifugal pumps, classification methods are common in the following ways 1 by the impeller inhalation points: single suction centrifugal pump double suction centrifugal pump. 2 according to the number of impeller points: single-stage centrifugal pump multistage centrifugal pump. 3 according to the structure of the impeller: open impeller centrifugal pump semi-open impeller centrifugal pump closed impeller centrifugal pump. 4 according to the working pressure points: low pressure centrifugal pump medium pressure centrifugal pump high pressure centrifugal pump side vertical centrifugal pump. Pipeline pump to use the five main points: 1, the test work: check the connector is loose; hand-cranked coupling so that the rotor turns a few times to see if the unit rotation is flexible, whether there is noise and uneven feeling, to determine the pump Is there a foreign body or the shaft is bent or not, the seal is installed incorrectly; Check the seal cavity clean No. 20 lube is filled with 1/2 cavity space; pump unit surface is clean; unit to no-load test. 2, manual start: filling pump (for the first time), slightly open the outlet valve, start the motor, the pressure rises and confirmed as the pump group running steadily outlet valve to the working conditions. 3, running check: pump in the normal frequency (frequency) normal operation, should regularly check and record the pump group ammeter, voltmeter, import and export vacuum gauge, pressure gauge and flow meter and other instrumentation readings. Unit vibration, noise, temperature rise is normal. Shaft seals should not have significant aviation fuel leaks. 4, normal parking: close the discharge valve, the pump light load, stop the motor. 5, emergency stop conditions: ⑴ pump motor current meter anomalies (too large or become too small); pump system abnormal sound. ⑵ pump inlet vacuum pressure gauge, outlet pressure gauge indicates an exception, the pump vibration larger and issued a different sound, a serious decline in performance. ⑶ pump motor odor, leakage at the shaft seal aviation fuel, bearing temperature over 75 degrees and so on.
Cold Drawn Steel Bar is produced by hot rolled steel bar or wire rod to get smooth surface, more precision size, higher mechanical properties, which improves machining characteristics. It can also get various sections and sizes. So cold drawn steel bar is a better choice for machining users.
According to different steel grade, the production line is usually different. The Basic production line is as below:
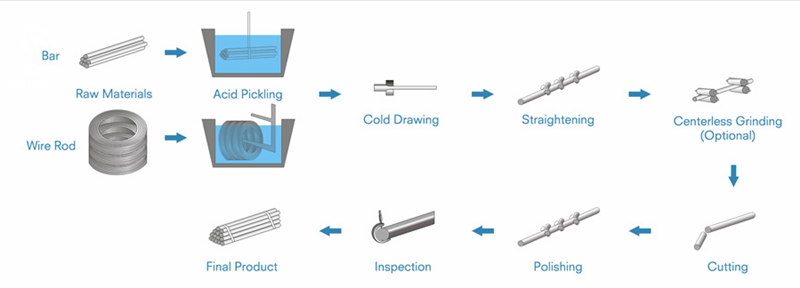
For high carbon steel or alloy steel bars, to avoid the cracks in inner or surface, the bars are usually required to be annealed before cold drawing.
To get different mechanical properties or hardness depending on final usage, the cold drawn bars will also be heat treated such as annealed, normalized or quenched and tempered(Q&T).
For CNC machines usage, to get much more precision sizes or much more better surface roughness for chrome plating, the cold drawn steel bars can also be centerless ground or polished.
We have more advantages on producing cold drawn steel bars:
1) Big stocks of hot rolled round bars or wire rods as raw materials
2) Wide range of cold drawn steel bar sizes: from 10mm to 150mm
3) Different cold drawing medias powder or oil to get different surface
4) Straightening machines to get better straightness up to 0.5mm/m
5) Grinding and polishing machines to get better roughness upto 0.4um
6) Heat treating furnaces to adjust the mechanical properties
7) Full sets of testing equipment to test the sizes, mechanical properties and microstructure.
8) Multiple packages to avoid broken packages and anti-rusty
Cold Drawn Steel Bar
Cold Drawn Bar,Round Steel Bar,Cold Drawn Steel Bar,Aisi 1018 Steel Square Bar
SHANDONG LE REN SPECIAL STEEL CO., LTD. , https://www.lerenspecialsteel.com
没有评论:
发表评论